Discover the latest developments from Tsubaki in the world of Drive and conveyor chains. This article provides information about innovative new products, shows their efficiency using user examples from the wood industry and automotive engineering, and presents you with exclusive service offers. Learn how to be eco-friendly roller chains Optimize your production processes in every industry and so on Reduce TCO costs.
Content:
- Environmentally friendly drive and conveyor chains with configurator
- Applications
- Titanium chain for wood mills, stone saws or brickworks
- Conveyor chain for hanging conveyor in body assembly
- Long-lasting roller chains for the rough timber industry
- High-tech lifting chain for a reliable buffer tower in steel construction
- Conveyor chain for triple service life in fiberglass wool production
- Tools & Service
Environmentally friendly drive and conveyor chains with configurator
December 14.12.2020, XNUMX | With a new approach to Product development and product design supported Tsubaki its customers in reducing the environmental impact in their operations and increasing their profitability. With the Eco + Eco, optimized for ecology and economy Drive and conveyor chains the efficiency of plants can be increased and resources recycling and reusability improved. A chain Configurator also facilitates the design of the individual conveyor chain.
Tsubaki has introduced a guideline for this with environmental requirements for all specially developed products. The drive specialist has the associated requirements as common development goals for the Eco + Eco range formulated.
Requirements for Eco + Eco chains
Jake Yamamoto, Sales & Marketing Director of Tsubakimoto Europe BV, comments: “The entire Tsubaki Group has been working together for some time with the aim of ensuring that all new developments are environmentally friendly. We have divided the controllable, ecological factors into the following seven categories:
- Resource conservation with waste reduction
- Energy saving with reduced CO2Emissions
- clean working environment
- Respect for the environment
- easy disposal
- reusability
- Pollution reduction.
By using these categories as the basis for overall design and product development and combining them with the demonstrable economic benefits of our products, we are fulfilling our obligation to our customers so that they can do theirs with our products Ecology and economy can reconcile ”.
All Tsubaki chains are already made with the Eco + Eco philosophy including the maintenance-free Lambda chain GT4 winner chain, the corrosion-protected Neptune chain and the G8 high-performance chain. All Necklaces offer a doubling of the service life compared to conventional chains and 49% less CO2Emissions.
Application conveyor chain for brewery barrels
Tsubaki demonstrates the potential of the Eco+Eco design in an application in one Brewery. 18 conveyor belts are used here to transport pallets with barrels. Each conveyor belt is 9,75 m long. A Electric motor with an output of 7,5 kW drives a triplex chain at a speed of 15 m / min.
Conveyor chain with 5 instead of 2 years lifespan in a large bakery
So far have used lubricant Pallets and barrels dirty. As a result, they were broken, contaminated and, in the worst case, even rejected. By doing without chain lubrication, the brewery tried to solve the problem. The result did not bring the desired success. The conveyor chains got stiff after a few months, the rollers worn out, the vibration increased significantly, the motor got too hot and caused a constant thermal error message.
The Tsubaki experts then recommended replacing it with a lubricant-free one Duplex roller chain. Their rollers cause less friction and are maintenance-free. To drive the conveyor chains, only a motor output of 1,5 kW was required. The downsizing also reduced energy consumption from 27.000 kWh to 5400 kWh. In addition, the CO decreased2-Emission dramatically from 15.255 kg to 3056 kg. The lifespan of the chain, however, increased from 4 years to around 15 years.
Configurator for the individual conveyor chain
Tsubaki now makes it easier to design with a chain configurator BS / DIN and ANSI simplex conveyor chains. With the Tsubaki Chain Configurator everyone can design their optimal chain with attachments around the clock. The chain configurator offers a variety of design options and the possibility of formatted 2D and 3D CAD models to export.
The chain options can be changed via Drag and drop choose. During the design process, the transport chains can be viewed from all angles, including the integrated components. In addition, the configurator provides measurements for the total length as well as specific sections of the chain.
After a chain design has been customized, the user can enter a 3D model Create, select and download a 2D or 3D CAD file in a variety of formats. Drafts can also be saved as PDF and printed. Finally, an offer can be requested.
The configurator is available in German, English, French, Spanish, Portuguese, Polish, Russian, Dutch and Italian. The new Tsubaki Chain Configurator can be tried out using the QR code.
Titanium chain for wood mills, stone saws or brickworks
October 15.10.2020, XNUMX | Tsubaki introduces his new one Titanium drive chain in front. It offers previously unattainable wear resistance in harsh operating environments. The titanium chain easily withstands extremely abrasive and dusty conditions such as in wood mills, stone saws or brickworks.
The drive chain combines the properties of the Premium GT4 winner Tsubaki chain with high wear resistance. Precisely manufactured, seamless bushings with integrated lubrication grooves and coated bolts are the special features in the production of the chain.
Thanks to the special Oil grooves the oil reaches the point of contact where it is needed most. The specially coated bolts offer an extra hard, yet low-friction surface. The combination of these bolts and the perfectly cylindrical bushes with lubrication grooves reduces the friction between the bush and the pin to a minimum.
Titanium drive chain lowers TCO costs
With the use of titanium chains, users can reduce their maintenance effort and system downtimes. The Total Cost of Ownership (TCO) are noticeably reduced.
Molded release film prevents galvanic corrosion in the car
Nickel-plated outer plates in combination with the inner plates made of a black oxide layer offer additional protection against corrosion. A special Stamping ring compression allows the titanium chain the full load-bearing capacity of the basic chain. The compression ring compression is patented.
The drive chain is available as standard in sizes 12B to 32B. Other sizes, multi-strand versions and attachments are available upon request. The company's research and development team developed the titanium chain at the Kyotanabe Technical Center Japan with the involvement of Tsubakimoto Europe BV. The development took place under the Eco & Eco TSUBAKI Group's approach.
Applications for conveyor and drive chains
The following two applications illustrate the usefulness of paying a little more attention to the chain. Total Cost of Ownership can be safely reduced. But read for yourself:
Conveyor chain for hanging conveyor in body assembly
January 14.01.2020, XNUMX | A British one Automobile-Manufacturer had a problem with the maintenance of the conveyor chains that his Hanging strap drive. This is used to transport the assembled carBodySilo equipment. The roller chains had to be replaced too often, otherwise they would have brought production to a standstill. By converting to a special conveyor chain from Tsubaki the problem could be solved. Only they had to Total Cost of Ownership (TCO) instead of the purchase price.
During the Automobile assembly the machines and systems used must run 24 hours a day all year round. Otherwise, downtimes can quickly cost thousands of euros per minute. Unfortunately, many people in charge see them Drive chain still appear as a product and make their purchase decisions based on price. You would be better off also throwing performance and quality into the balance.
Small conveyor chain with a big impact
During the Body assembly of cars, overhead conveyors often move the car parts from one workstation to the next. The conveyor systems driven by conveyor chains thus represent an important part of the material flow. If a conveyor chain fails, a large part of the production line comes to a standstill over several process steps. Special chains offer a much longer service life than standard chains - especially when it comes to high-performance applications.
Also one of the UK's largest Automobile-Mounting plants had this problem. The in the Overhead conveyor The built-in chain had to be replaced every twelve months and serviced every three months. To be on the safe side, the conveyor chain was lubricated every three months. Nevertheless it became stiff and stiff. In addition, dust particles caused pollution. That led to wear and tear. The conveyor chain usually broke before the end of the twelve months.
Change to special conveyor chains recommended
The operations manager had to change that and turned to the leading manufacturer of drive technology products, Tsubaki. The experts found that the OE versions originally installed were not suitable for high-performance operation. So they suggested the OE chain through a Quality chain to replace.
Reading tip: Select roller chains correctly
In addition, the new conveyor chains should offer added value for the production line and lower total operating costs Total Cost of Ownership (TCO). The Tsubaki engineers then recommended switching to a maintenance-free, self-lubricating chain for the Lambda-Series. This means that manual lubrication is no longer necessary. This reduced maintenance costs and downtime.
In order to further increase the service life of the roller chains, the engineers developed a special cover plate, which was attached to every other chain link above the pins. This reduced the contamination of the chain links and protected the chain rollers from wear. The rivets used to attach the cover plates to the bolts were replaced with high-strength screws held in place with a locking adhesive.
After comparing products and replacing the chains, the conveyor system usually works reliably for more than two years. This is more than twice the lifespan of the OE conveyor chains.
Long-lasting roller chains for the rough timber industry
May 29.05.2019, XNUMX | Tsubaki presents a wide range of drive and conveyor chains, which have a longer service life than comparable drive elements. The standard roller chain “GT4 Winner” is manufactured according to BS/DIN standards and has high strength and easy handling. The low-maintenance "Lambda" chain in the sixth generation based on the GT4 Winner does not need to be relubricated.
One with lubricant vacuum-impregnated sinter bushing ensures a sufficient lubricating film in the chain joint. The “Neptune” chain is also based on the principle of the GT4 Winner. It is suitable for humid environments where greater corrosion protection is required. For the "Heavy Duty" chains, the world's best steel materials were selected and the individual chain components were coordinated with one another in such a way that a whole range of different heavy-duty chains was created.
Their higher strength and better wear resistance are in demand in the highly stressed drives of woodworking plants, as homogeneous and smooth processes cannot be assumed when processing the still raw wood. In addition, a variety of angle and (special) Driving tabs realize almost all customer-specific requirements placed on a conveyor chain.
High-tech lifting chain for a reliable buffer tower in steel construction
May 24.05.2018, XNUMX | In this application a Dutch could Steel mill thereby increasing the productivity of its heat treatment in the long term. How? By replacing Tsubkaki with his fail-prone drive chains High-tech lifting chain with a service life of up to 15 years.
Conveyor chain for triple service life in fiberglass wool production
January 31.01.2017, XNUMX | A manufacturer of insulating fiberglass wool found out that premature wear of the components installed in a conveyor system conveyor chain was responsible for the declining product quality. He replaced the chain with a premium chain from the leading manufacturer of drive technology products Tsubaki.
Tools and service
Of course, Tsubaki not only offers drive or conveyor chains and other drive elements, but also provides its customers with the appropriate service and accessories, as these examples show:
Service ensures synchronicity of roller chains operated in parallel
February 12.02.2018, XNUMX | Do chain strands in machines have to be in pairs or multiple parallels? operated synchronously it is necessary that the drive elements have exactly the same length. To ensure this, Tsubaki offers the optional “Match + Tag” service. This ensures that the chain strands have a maximum length difference of 0,5 mm.
If chains are operated in parallel and synchronously for conveying purposes and the chain strands are not coordinated with the necessary synchronism despite the same nominal length, problems like this can occur Twisting or a slip during operation. This problem can worsen over time as the chains wear out. An assembly that initially works becomes increasingly more prone to problems. The result is a chain exchange earlier than expected.
The Match + tag service makes sense because industry standards specify a tolerance range for the chain length, but do not contain any information regarding the composition of chain sets for chain strands installed in parallel. Chain strands manufactured based on these standards can therefore differ significantly in their overall length if chain links with different tolerances are used.
The Match & Tag process begins after the Chain assembly with a precise length measurement of the chain segments. The chain segments are then assigned by length and labeled as pairs or larger groups. The service is immediately available for the following chains: BS short link chains in sizes RS08B to RS32B, ANSI short link chains in sizes RS40 to RS100 and ANSI long link chains in sizes RF2040 to RF2100.
Chain wear gauges for roller chains
04.12.2018/XNUMX/XNUMX | If the chain drives in systems are checked regularly, one can timely exchange the roller chains installed in it prevent unexpected failures. Tsubaki has expanded its range of chain wear gauges to include large sizes for the maintenance of such chain drives. The new chain wear gauges have been created for the BS sizes RS20B to RS48B and the ANSI sizes RS100 to RS240.
They complement the BS and ANSI set with sizes RF06B to RS16B and RS35 to RS80. The chain wear gauges meet the highest quality requirements and are corrosion-resistant. Their robust construction ensures accurate measurements at all times over a long service life. All chain wear gauges are also available individually.
Wear and tear Elongation of the chain results in loss of alignment accuracy for the entire drive system. This is particularly noticeable in positioning and locating tasks, reduces efficiency and increases noise and vibrations. If wear exceeds a critical point, the chain begins to rise in the sprockets or even jumps out. The result is shock loads with even more wear.
Such Problems are avoidedby regularly checking the chain for wear elongation. With the practical gauges, the condition of roller chains can be measured and their degree of wear can be determined in just one operation. The wear gauge works according to the traffic light principle: the chain is as good as new when the wear is less than 0,7%. Then the tip of the display bracket does not fit between the rollers of the chain. The degree of wear is acceptable with elongation between 0,7 and 1,5%. Here the green area of the display bar rests on the chain. The chain must be replaced if it is elongated by more than or equal to 1,5%. This is displayed when the red area reaches the chain link.
You might also be interested in...
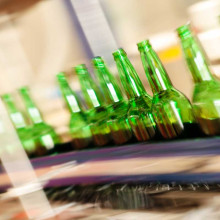
Roller chain for the high demands of food technology
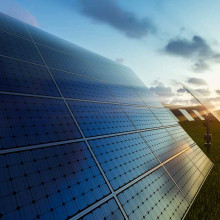
Flexible solar modules, rotating solar panels and other photovoltaics
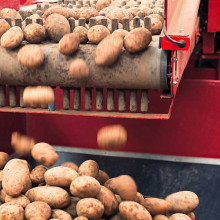
Potato harvester reliable again after conversion from freewheel
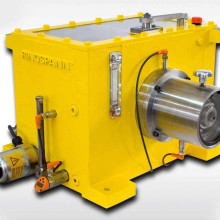
Freewheel clutch | Backstop and overrunning clutch
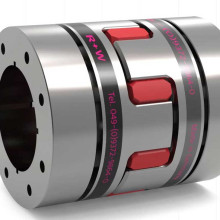
Claw coupling | With elastomer as a performer
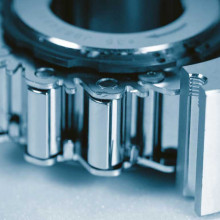