With the strong increase in e-mobility, a topic that is gaining in importance in the Automotive industry Although it has always played an important role, in practice it was played out in secret: thermal and mechanical Put or joining of sheets, assemblies and components. Tox Pressotechnik offers with the e clinching a process that takes account of increasing electrification.
In the course of electrification New challenges arise, especially with regard to electrical components, for example conductivity, stability and security of the connections under all conceivable vehicle operating conditions. Mechanical clinching has its origins in the Tox round point joining process. This involves a cold forming process that results in a force-fitting and positive connection that offers optimal electrical conductivity.
Conveyor chain for hanging belt for the transport of body parts
An essential aspect of the reliability and future viability of e Clinching is the special training of the Joining zoneBecause the sheets to be connected flow into one another, in addition to the form and force fit, also a material fit in the form of metallic micro-contacts. The high electrical conductivity of the clinch connections for a wide variety of Materials was confirmed in various analyzes and investigations by neutral institutions and consequently the joining process was transferred for applications in industry.
Product range expanded through e clinching
Among other things, an automobile manufacturer decided in favor of this technology and awarded it to the South Tyrolean technology company and supplier Intercable GmbH from Bruneck, Italy, the approval for the assembly of fuse boxes to connect their current-carrying components by Tox Pressotechnik e clinching. As a development partner, Intercable works together with automobile manufacturers on new solutions for joining sheet metal in the field of hybrid cars and electric vehicles. Through the e Clinch technology or by means of Enforcement joining Intercable's range of products and services has been significantly expanded.
Intercable commissioned the company with the design and manufacture of the production system required for series production AKE Technologies GmbH in Passau, which in turn brought the clinching specialists from Tox on board. The scope of the order included both the design of the clinch Tools as well as the corresponding manufacturing technology equipment. AKE Technologies received a total of 12 ready-to-connect TOX clinching pliers, depending on the type and design of the assembly fuse box individually or in blocks with up to three system units were integrated into the various modules of the production system.
Technology and production equipment from a single source
Designed as Single point pliers With an adjustable die, the pliers systems consist of a standardized Tox pliers type TZ with ram guide and a throat of 300 mm, a punch-side drive, a punch-side scraper including Tox tool check, the Tox control STE with process monitoring and the Tox clinch tool (punch and die ).
Select eyebolt, cotter pin, axial joint online
For the needs-based, reproducible, exact generation of the required Pressing force A servomechanical Tox Electricdrive drive unit of the type EPMR 055 provides for pressing forces up to max. 55 kN is designed. Furthermore, the system and scope of delivery include Tox spray systems of type SP to ensure the lubrication required during the joining process. cableset and the associated test reports complete the scope of delivery.
All of the sheets to be joined consist of Copper in very different thicknesses with 0,40, 0,60, 1,00, 1,50 and 2,50 mm, whereby the joining partners z. B. with a thickness of 2,50 mm on the punch side and 0,40 mm on the die side can be very different. Depending on the joining partner or material thickness, the clinch points have a diameter of 6 or 8 mm, which ensures very good and reliable electrical conductivity thanks to the full-surface metallic microcontacting.
Also suitable for demanding applications
Using the example of report Data on a clinch connection between two joining partners made of copper make it clear that e clinching is also suitable for demanding joining operations: component thicknesses on the punch side 2,5 mm and die side 0,6 mm, pressing force including hold-down force 23 kN, point diameter 6 mm, die depth 1,6 mm, remaining floor thickness control dimension X = 0,75 mm.
Another eight combinations of the Joining partner are feasible. With the identically equipped clinching pliers selected as standard equipment and the max. Servo drives generating 55 kN pressing force have enough reserves to join further e-assemblies - this in the sense of a rational, flexible production of variants aimed at the future of the automotive industry, which will represent another ongoing challenge for the industry and its suppliers in addition to e-mobility.
You might also be interested in...
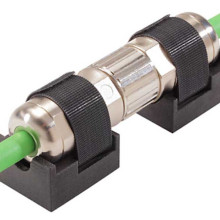