As late as possible, as early as necessary: This is the formula for the optimal time to replace filters in high and medium pressure hydraulic filtersto ensure trouble-free operation in hydraulic systems. A new two-stage contamination indicator from Stauff lowers the costs for the user Hydraulic system, The revised version of type HI-D024 considerably simplifies checking the contamination status of the filters.
The user exchanges the hydraulic filters in the plant too early, it causes unnecessary maintenance costs and also wastes resources. If he waits too long, he has to reckon with performance losses in the hydraulic circuit because the differential pressure in the filter rises to a level that negatively affects the performance of the system. In the worst case, the filter completely loses its performance, which can endanger the function of individual components and lead to expensive downtime of the entire system.
Hydraulic cylinder in tie rod and block version, linearly damped
Compared to the previous model, the new version can output four instead of two optical alarm messages - from green (everything OK) to yellow and orange to flashing red (filter saturation reached).
How does the clogging indicator work?
The user recognizes at an early stage that the differential pressure approaches a critical value and has the opportunity to react accordingly. In the event that he does not act and the factory-set differential pressure value of 5 bar is reached by 75%, a signal is sent that z. B. serves as an advance warning to the machine operator or the responsible maintenance specialist. When 100% of the defined differential pressure is reached, the system can be automatically switched off via a second output signal.
In addition, the Temperature of Hydraulic System Liquid determined. This prevents false alarms, which can be caused by the high oil viscosity in the cold start phase. This new thermostop function is issued as a further visual alarm (in blue).
Microprocessor controlled pressure switch
The degree of pollution - that is: the differential pressure before and after hydraulic filters - is controlled by a microprocessor pressure switch determined. To trigger a switching process, the corresponding pressure must be exceeded for at least 4 s. Malfunctions due to brief pressure peaks can thus be effectively avoided.
Reading tip: Rollon | The engineering partner
In the course of the development, Stauff's engineers were also able to minimize the dimensions of the display tool - despite the additional functions for the careful cleaning. This is another reason why existing systems, in which pressure filters have so far been used entirely with or without a conventional, single-stage contamination indicator, can easily be retrofitted.
You might also be interested in...
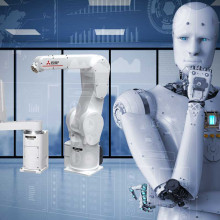
Predictive maintenance for robotics, machines and systems
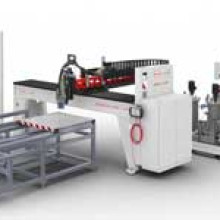